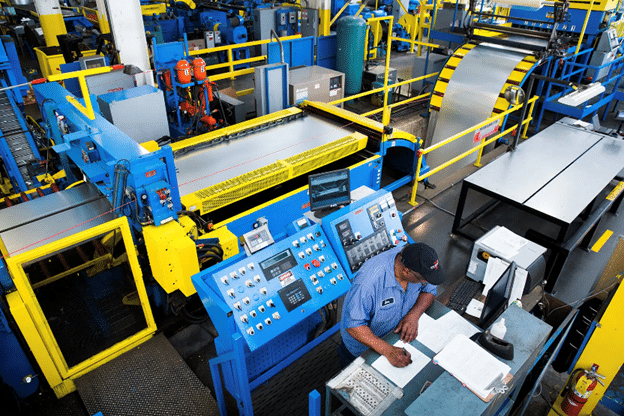
6 Common Steel Defects Encountered in Quality Assurance
Steel plays a crucial role in our modern world, finding applications in various industries. To maintain high-quality standards, it’s essential to recognize and understand common steel defects and how to